Digital Transformation Readiness: 7 Steps To Prepare For IIOT and AI
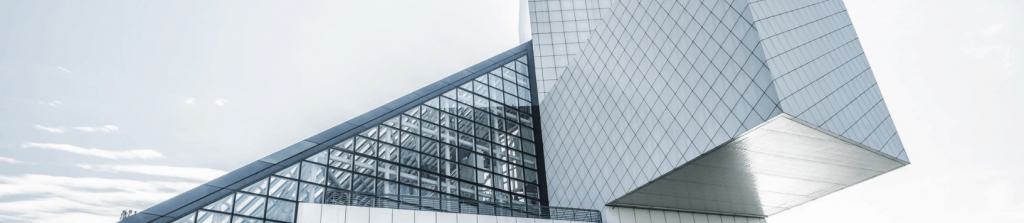
Is your organization prepared to reap the benefits of modern digital manufacturing?
Manufacturing today faces many challenges including rising operational costs, operational inefficiencies, reduced budgets and the requirement to release products faster. Digital technologies such as AI, cloud, and analytics can enable manufacturers to create a differentiation due to increased productivity and reduced operational risk, while improving product quality and customer satisfaction.
However, many business processes in todayโs manufacturing environment are often full of information gaps. Many large organizations find themselves paralyzed by old IT architectures or legacy systems with the inability to effectively manage manufacturing processes involving multiple data-sets between the shop floor and the back office.
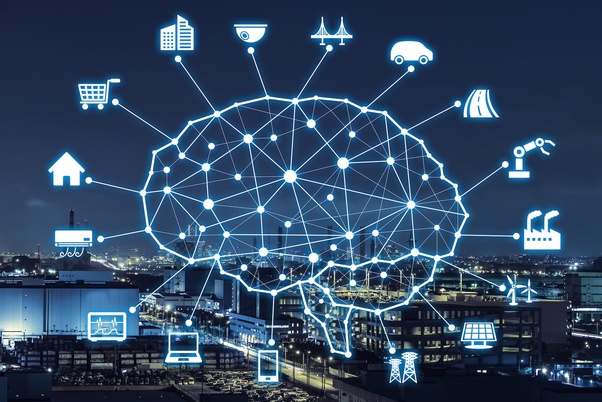
Here is a checklist of preparedness for industrial internet of things (IIOT) and AI that can help assess your organization’s ability to support the factory of the future:
1. Do you have paper-based processes?
You might be surprised that something as complex as sourcing components from multiple suppliers and sister factories, including products with long lead times, is still being done using Excel. However, relying on paper processes will prevent the ability to synthesize information from multiple data sources, and to calculate, communicate and compare key performance indicators (KPIs) to continuously improve productivity.
2. Are there manual processes that could benefit from automation?
In many cases, manufacturers still rely on manual processes for quality control and auditing to measure compliance to regulations. Automation is essential not only for saving man hours and reducing product defects, but also for providing the necessary flexibility to adjust to the rapid rate of changes in regulations and new product requirements.
3. Do you have a complete real-time view about shop floor operations for pre- and post-production?
Many manufacturers suffer from too many operational inefficiencies, such as delays, false starts, and rework, that can be avoided by using real-time data to make better decisions. By using IoT to automatically collect operational data and AI to analyze the results, manufacturers can improve the accuracy of real-time decisions and minimize risk.
5. Have you created new business models based on your digital transformation activities?
There are many new business processes that are enabled due to improved ways to collect, share, and analyze production data. For example, operations can be monitored and even controlled remotely. Different processes or departments operating in silos can collaborate better to create more efficiency and value. Consumer packaged goods companies can detect and reduce theft by tagging and tracing products throughout the supply chain. With the advent of IIoT and AI there are countless new ways to use connected operations for differentiation and advantage, but before the technology can be put in place, the new business processes need to be identified and analyzed. This is an opportunity for enterprises to bring their business to the next level, providing new revenue streams, value producing opportunities, and growth โ in order to differentiate from their competitors.
7. Are you still relying on hard-coded connections between systems?
Hand-coded system integrations can be more resource efficient in the beginning, since projects are limited in scope and often internal resources can be used. But, in time, these projects can multiply rapidly and become unwieldy as more and more systems become part of a manufacturerโs information network. A more resource efficient and practical solution can be a multi-point third party software platform that provides scalability and proven unified data handling for all of the integrated systems.
4. Are you systems integrated, end-to-end, including ERP,CRM, MES etc…, to increase productivity?
To support the factory of the future there needs to be a manufacturing environment in which shop floor and back office systems can communicate easily and offers real-time access to critical data anywhere in the supply chain on any system. A steady stream of performance and production data needs to be collected, stored, analyzed and shared efficiently, reliably and securely. When systems can communicate seamlessly together an end-to-end process can be optimized. For example, when MES and ERP systems are fully integrated and there is an equipment problem, replacement parts can and a service ticket for a qualified technician can be generated automatically.
6. Are you fully utilizing your data, or is stuck in a data swamp?
For many plant managers, the increase in data as a result of IIoT just makes more work. Deployment of sensors to monitor machines and products provides vast opportunities for automated collection of operational and supply chain data.
According to a recent survey, โ80 percent or more of production systems contain legacy equipment never designed to communicate beyond the plant floor.โ Driven by the need for real-time access to critical data from various data sources as well as collaboration across the supply chain, more and more manufacturing software applications are migrating to the cloud and using advanced and predictive analytics for better operational intelligence. This includes processing data from various data sources, which allows discovery of unexpected failure and events, more accurate decisions in real time, reduced operational risk, and a better understanding of customer behavior.
The Advantages of AI and IIot will only increase as technology matures and more use cases are developed.
However, before advanced technologies can be implemented, processes need to be automated and systems need to be connected. To reap the benefits of the age of modern digital manufacturing, new business processes that can benefit from shared information need to be identified and analyzed. Once the relevant business processes are digitized, an IT infrastructure for sharing and analyzing production data can power the factory of the future. The digital disruption is happening now.