5 Facts You Should Know About Predictive Maintenance
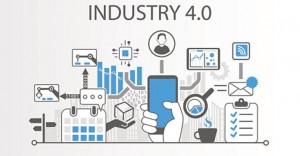
Predictive maintenance is not new, but today more then ever, with advancements in technology, predictive maintenance can result in significant savings for manufacturers.
By utilizing sensors to monitor operational conditions, storing historical data in the cloud and performing analytics,ย predictive maintenanceย makes it possible to service equipment based on actual wear and tear instead of scheduled service visits, thereby preventing the possibility of downtime. Machines on the factory shop floor can even evaluate their own performance and order their own replacement parts and a field technician when necessary.ย A more advanced version ofย predictiveย maintenanceย can even use algorithms based on big data to predict future equipment failures.
There is a huge incentive to invest inย predictiveย maintenanceย solutions, because their positive impact on a factoryโs operating efficiency has a significant influence on the bottom line.
Here are five facts that show how predictive maintenance can improve manufacturing performance
A Joint Study
byย Wall Street Journal and Emersonย found that unplanned downtime costs industrial manufacturers an estimated $50 billion per year. Equipment failure is the cause of 42% of this unplanned downtime. In addition to the loss of productivity, unplanned outages result in excessiveย maintenance, repair, and equipment replacement costs. Outdatedย maintenanceย procedures not only waste resources, they can expose factory floor workers to a greater safety risk.
The Costs
of interrupting operations continue even after production begins again. Half of all large companies face quality issues after an unplanned shutdown according to theย Customersโ Voice:ย Predictiveย Maintenanceย in Manufacturing reportย by Frenus.
Reactive Maintenance Work
costs four to five times as much as planned service calls that proactively replace worn parts. If equipment fails because there is a lack of awareness of degraded performance there are immediate costs due to lost productivity, backup of inventory, delays to completing the finished product, operator labor to rework the part, and more.
Predictive Maintenance Costs
ย $9 hourly pay per annumย while preventiveย maintenance, servicing equipment based on equipment life and manufacturersโ recommendations, costs $13 hourly pay per annum. When parts are only replaced at the optimum time, not when itโs too late after the part has failed, or too soon when the part is still in good working condition there are large cost savings in terms of labor, equipment life and avoided downtime.
Data From the US
Department of Energyย indicates thatย predictiveย maintenanceย is extremely cost effective. Putting a functionalย predictiveย maintenanceย program in place can yield remarkable results: a tenfold increase in ROI, 25%-30% reduction inย maintenanceย costs, 70%-75% decrease of breakdowns and 35%-45% increase of up-time. Despite the clear advantages ofย predictiveย maintenance, factories today are still investing more in preventativeย maintenance. In one study, 45% of assetย maintenanceย was shown to be preventive, 40% reactive and only 15%ย predictive.
However, despite the financial benefits and the consensus thatย predictiveย maintenanceย has a strong pay back, there are obstacles in the way. The sensors need to be able to monitor conditions with a high level of reliability in real time to provide meaningful data and some sensors still have antiquated technology.
There needs to be a high level of data integration, and that brings with it a whole new set of complexities especially when connecting the back office to the front office.
There is a need to integrate separate solutions from different product manufacturers in order to create one unified workable solution to manage the factory floor. These systems need to share data with ERP and logistics systems to automate an end-to-end business process for equipmentย maintenance. Data needs to be collected and shared with a high level of security to protect manufacturersโ intellectual property and the financial and personal data of their customers.ย With all the sensors monitoring equipment condition, fluid quantities, vibrations and heat there are vast amounts of data that need to be collected, stored and analyzed. Any data management solution needs built-in scalability to collect, filter, process and share huge volumes of data with a high level of performance and reliability.
Despite the technological hurdles,ย predictiveย maintenanceย is an essential part of the factory of the future. Manufacturers who automate not only manufacturing processes but alsoย maintenanceย can benefit from a massive economic advantage by raising their factory to a whole new level of efficiency.
Originally Posted by Iot Central – https://www.iotcentral.io/blog/5-facts-you-should-know-about-predictive-maintenance?context=featured